The Aluminum T-Beam Electric Guitar
Recently, reader Alex G. shared several pictures of his innovative concept for an aluminum neck guitar based around an aluminum T-beam form. The idea definitely piqued my interest and I’m glad to learn that Alex has joined the ranks of guitar bloggers with his own site The Aluminum T-Beam Guitar. There he intends to document his guitar project which will, of course, be based on an ergonomic guitar shape. 🙂
Although his guitar blog is only a few days old, Alex has already published two excellent articles. The first, Background – Why and How explains how he became interested in this approach and contains renderings illustrating the basic concept. This exploded view of a guitar based around the T-Beam neck concept does a great job of explaining his intended approach:
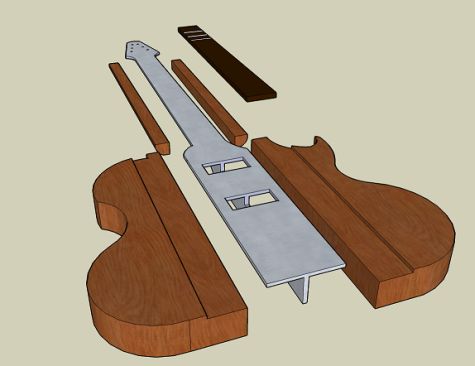
The second article, Guitar Ergonomics, discusses his decision to make an electric guitar based on an ergonomic shape. Alex notes both the Klein Electric Guitar and the Forshage Electric Guitar as influences for the shape. Here is an early image that suggests what we can look forward to:
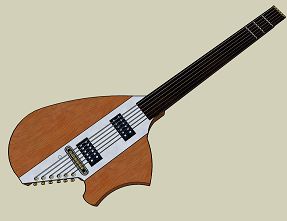
Overall, I’m excited to see innovation among guitar makers. The unfortunate truth is that the typical guitar project is a rehashing of the Strat, Tele and Les Paul shapes with a few minor detail changes or a different choice in wood. With Alex’s guitar build, we see a willingness to experiment with both the basic construction of the guitar as well as the choice in body design. Thank goodness! I, for one, will be watching Alex’s guitar project very closely.
BTW, don’t forget to check out these other guitar builds by Building the Ergonomic Guitar readers:
You know me…eric the “traditional” guitar builder.
this is an interesting concept, it looks like it would be really stiff. It may have a completly different feel with an aluminum reinfoeced neck through design.
He may want to dump the wood and with the an aluminum neck and fiberglass cast body. He could do come really cool shapes, and color combos,and it would weigh next to nothing.
Interesting idea, Eric. I’ve been thinking about composite materials for a guitar project down the road and fiberglass and carbon fiber keep popping into my head. I’d love to see just how light one could be made although I have a feeling that there may be some concerns around balance due to it ending up neck heavy. Of course, its not an insurmountable problem.
The fibreglass body (and neck pieces too) is a really good idea. It’s a bit strange to me though… I envisaged the guitar in wood and aluminium quite early in the planning and never gave alternatives much consideration. I think I had the old-fashioned sports cars steering wheels in mind – as e.g. these these, with their combination of wood and metal.
But why not? It could be beautiful in a very different way. And the sound would probably be a very pure bell-like aluminium sound without the wood.
Unfortunately, I have no experience in working with fibreglass, so I’ll stick to wood for now.
/Alex
How is the tuning stability of the aluminum?
Compared to wood, it expands and contracts more with temperature, which can be a problem. On the other hand, it is indifferent to moisture.
Regarding its strength, I believe the neck is strong enough to resist the pull of the strings without curving too much (and detuning strings). If not, I’ll have to install a truss rod (actually two; one on each side of the bottom flange).
/Alex
Very interesting. 🙂 I’ll be keeping my eye on this one.
One thought I had over the weekend…Try to integrate the T-rod into the design of the aluminum frame. design a threaded hole at the body end…big enough to take a steel heli-coil insert. Lower the overall profile of the rib down the length of the neck so the rod could work in the traditional fashion.
You mean let the truss rod rest on the bottom rib? Good idea, especially if making thin shell fiberglass body and neck pieces (where the neck piece would be one piece covering the whole back of the neck). I still don’t think it will be necessary, so I’ll make the guitar without it. But if the neck turns out to be too weak, it is a useful solution.
I would be interested to hear someone’s opinion about the fact that sound will travel through metal much more quickly than through wood. How will the difference between wood and aluminum interact with respect to the velocity of sound?
I’m imagining that you may end up with a more or less conventional sound due to the absorption of frequencies by the choice of fingerboard wood. Or, perhaps the guitar will sound very bright if the aluminum “top” reflects virtually all of the strings’ frequencies.
Is sustain the principle design goal here? If so, there will have to be something in the choice of material for the “T” that not just transmits sound efficiently. It would have to also feed some of the vibrating strings’ energy back to the strings to keep them vibrating longer.
Thanks for the very interesting questions. Let me say for a start that I’m building the guitar hoping and assuming that the combination of wood and aluminium will give a good sustain and a clean sound (though not as bell like as pure aluminium guitars such as the Bergeron [http://www.bergeronguitars.com/]). I expect to attempt swapping various body “wings” and necks of different species and shapes on the aluminium t-beam in order to strike a good mix between the woody and “aluminiumy” contributions to the overall sound.
I’ve tried to address your individual points below.
“I would be interested to hear someone’s opinion about the fact that sound will travel through metal much more quickly than through wood. How will the difference between wood and aluminum interact with respect to the velocity of sound?”
I would like to know a more about that as well. I have no clear expectation. If the result turns out bad, I might mount the wooden parts (body “wings” and neck halves) on a few contact points instead of having large surfaces touching one another. That should help keeping the wood somewhat more out of the equation. …a bit like the principle of the metal cones you use for reducing the transmission of vibrations from speaker cabinets to the floor.
Alternatively, the fibreglass approach suggested in an earlier comment would be interesting.
…but regarding the question: I have no scientific knowledge on the subject. But other people have created great sounding guitars with combinations of wood and aluminium.
“I’m imagining that you may end up with a more or less conventional sound due to the absorption of frequencies by the choice of fingerboard wood.”
I partially agree. But if it turns out just “less conventional” (as opposed to more conventional or perhaps completely ordinary), I’m satisfied. I hope for a well-defined crisp sound, not a very sharp one.
I did consider cutting fret slots directly in the top aluminium flange, which would have resulted in the string vibrating in a “closed circuit” of metal (the fret, the aluminium top flange and the bridge). It would have bled some vibration to the wood of the neck and the body, but apart from that, I assume it would give very good sustain. I decided against it, as it would have been way too daunting a task considering my very limited experience in metal working and guitar building.
“Or, perhaps the guitar will sound very bright if the aluminum “top†reflects virtually all of the strings’ frequencies.”
It might. And that’s not what I’m aiming for. If I’m lucky, the rosewood fretboard will give a good combination of warmth and clarity. If not, I might experiment with other wood species – or altogether different materials such as plastic or metal.
“Is sustain the principle design goal here?”
Not exclusively. I also hope for a sound that is articulated over the whole spectrum – a “big” sound that is crisp as well as warm. Plus a very beautiful guitar.
“If so, there will have to be something in the choice of material for the “T†that not just transmits sound efficiently. It would have to also feed some of the vibrating strings’ energy back to the strings to keep them vibrating longer.”
The weak point will be where the fret rests in the rosewood fingerboard. Apart from that, the strings’ vibration is carried by a closed system of aluminium and nickel alloy (the fret). I don’t know how much that weak point will sap the string’s energy. But I hope that the strings will be able to vibrate without loosing energy too fast. Of course, having the frets directly in the aluminium would be optimal sustain-wise, but I expect the small piece of rosewood in the equation not to matter too much. If the rosewood fretboard – contrary to my expectation – is a case of “the weakest link in the chain”, sapping all the energy that is conserved in the metal parts, then I’ve got a problem 😉
Again, thanks for the very relevant and thought-provoking questions. Obviously, I don’t have all the answers myself, and the above can in no way be considered a final reply to the questions. I would welcome anyone with opinions of these issues to contribute their points.
Alex – Thanks so much for the detailed reply!
My pleasure.
I’m happy that people take interest in the project.
scalloped fretboards man,i would think the frets(stainless?)have to be connected to your T bar? awesome wat your doing,great bloody concept!!didnt Les paul start out with a neck and some screws.i like the potential as a home kit that dad n son can put togeather at xmas,or the pro can break it down like a gun and carry it anywhere…am i gettin carried…
Thanks for the support.
I never tried a scalloped fretboard. I am one of those people who keep pressing until I feel wood under my fingers, so I won’t do anything like that on this guitar. But it could be interesting, especially if I had the frets sitting in the aluminium.
The home kit potential also appeals to me. I think it’ll be quite an easy guitar to build once you know how to do it (which is what I am trying to find out these days). The T-beam takes care of structural strength, so the design is quite forgiving in many aspects. At least, so I expect. When I’ve built it, we’ll know more.
I’ve never though of it as something you could disassemble for easy transport. The removability of neck and body wings is more suited for experimentation with different shapes and materials, I think.
…but yes, it would look cool to be able to assemble the guitar from five or six separate pieces with a couple of *click*s 😉
…of course it would be way less cool, if it came apart with one large *clack* in the middle of a solo.
i think your on the right track…who dosnt want to try different body shape and neck profiles.Goodluck !!
That idea has come up before in the comments and I think it makes a good deal of sense. A neck thru would make a great platform for testing a variety of shapes. Bolt on wings and you’re in business. Although not quite the same, it reminds me of RKS Guitars which has a central “pod” contains the headstock, neck, bridge and electronics. The whole thing can be swapped in and out of bodies in a couple of minutes.
Wow, I don’t know why but it has taken me a while to find this post on your blog. I’m glad I did though. The blog that he created seems to be going well.
The current design is remarkably similar to something that I drew up about 18 months ago….minus the aluminum of course. I think its a great design which frees you up from having to be tied to specialized equipment.
I completely agree, Grand. I’ve covered a few alternative designs that make use of conventional bridges and tuners in a headless arrangement thus eliminating the dependency on specialized components.